Electrochemical Machining (ECM) | Get a Free Quote from BF&S Today
Electrochemical machining (ECM) is an advanced electrochemical process used to remove metal from workpiece materials without direct contact. Unlike traditional machining processes, ECM uses controlled anodic dissolution to shape complex and hard-to-machine metals with precision. This method ensures minimal tool wear and superior workpiece surface quality.
How the ECM Process Works
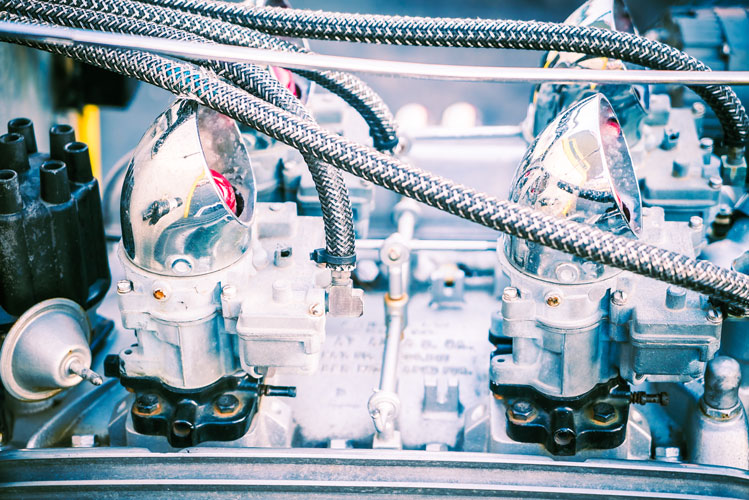
The electrochemical machining process relies on an electric current passing between a cathode tool and a workpiece material submerged in an electrolyte solution. As the current flows, metal ions dissolve from the workpiece through anodic metal dissolution, ensuring precise metal removal while shaping the piece into the desired shape. The electrolyte flushes away dissolved particles, maintaining process stability and preventing unwanted deposits.
Unlike electrical discharge machining, ECM generates no heat-affected zones, making it ideal for delicate and high-precision applications.
Electrochemical Deposition and Material Properties
In addition to material removal, ECM can enhance material properties through electrochemical processes like deposition. By controlling the electrolyte composition and current density, engineers can modify the surface characteristics of the workpiece material, improving corrosion resistance and durability.
Material Removal and Workpiece Surface Quality
The ECM process efficiently removes material at a microscopic level, ensuring high accuracy. Unlike traditional machining processes, which rely on mechanical force, ECM eliminates residual stresses and tool wear. The result is a smooth workpiece surface with precise dimensional control.
Benefits of the Electrochemical Machining Process
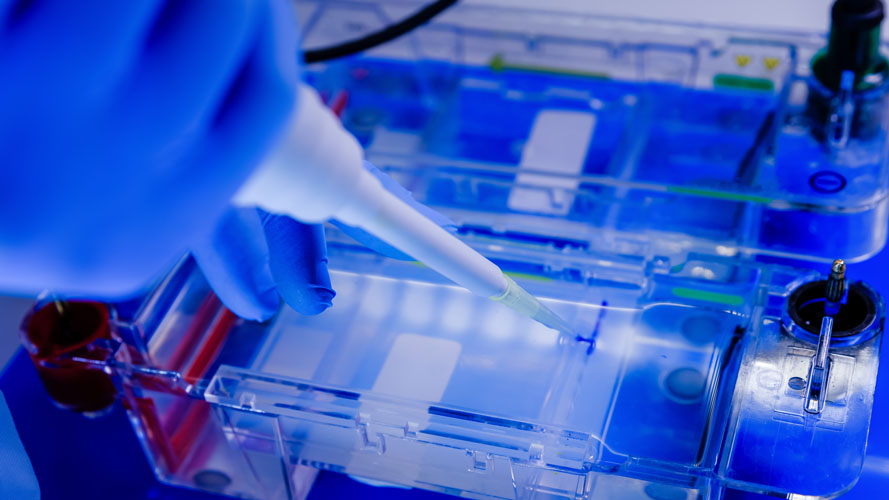
The electrochemical machining process offers several key advantages: ✔ No mechanical stress or tool wear ✔ High precision and complex desired shape capability ✔ Improved material properties through controlled dissolution ✔ Superior workpiece surface quality ✔ No heat-affected zones, unlike electrical discharge machining ✔ High process stability, ensuring repeatable results
Challenges of the ECM Process
While ECM provides many benefits, it also has some drawbacks: ❌ High initial investment and operational costs ❌ Limited to electrically conductive materials ❌ Requires careful electrolyte management to prevent corrosion ❌ Disposal of used electrolyte can increase costs
Why Choose BF&S for ECM Machining?
At BF&S, we specialize in precision machining processes using the latest ECM process technology. Our expertise ensures superior workpiece surface quality, enhanced material properties, and consistent process stability.
Whether machining turbine blades, medical components, or aerospace parts, BF&S delivers unmatched precision and efficiency. Visit the BF&S website today for a free ECM quote and experience unmatched precision in metal machining.